Ndfeb hydrogen decrepitation.jpeg.
High-temperature demagnetization can, however, cause melting of components, e.g., plastics, glue, etc. Hydrogen decrepitation (Table 8.3), a more efficient alternative, has been suggested for processing of HDDs [34], [35]. The NdFeB magnets absorb hydrogen, expanding in volume with about 5%, which causes breaking into …
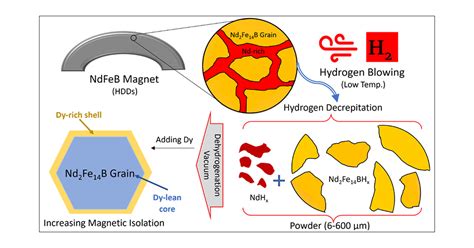
So exposure at LOW temperature to hydrogen leads the NdFeB pieces to react via intergranular fracturation (decrepitation), the mass of Nd2Fe14B grains forminfg a metal hydride with max ...Sep 20, 2016 · Hydrogen decrepitation of Pre-dismantled Computer HDDs. The University of Birmingham (UK) has developed a hydrogen-processing method to extract sintered NdFeB magnets from computer hard disk drives [13, 41]. During this process, either the voice coil assemblies from the hard disk drive or the cropped corner from the drive is exposed to hydrogen ... A bulk ingot of a Nd-Fe-B alloy has been powdered by a combination of hydrogen decrepitation and attritor milling. The powder was aligned and pressed in the hydrided condition and the green compact sintered at 1080‡ C for 1 h after an appropriate heating rate. Excellent densities were achieved after this procedure and the magnets produced …Keywords: Finite difference method; Kinetics; Hydrogen decrepitation; NdFeB alloys; Diffusion 1. Introduction Sv (V ) expansion due to decrepitation results in a five orders of magnitude higher rate of hydrogen diffusion into The most popular recent application of hydrogen in the Nd–Fe–B alloy than into a theoretical bulk sample of that ...
Magnetic powders for sintered NdFeB magnets have been prepared by using an advanced processing method including strip casting, hydrogen decrepitation, jet milling and rubber isotropic press. The effects of Dy, Ga and Co addition on the microstructure and magnetic properties of sintered magnets have been investigated. By adopting a suitable …In this paper, the hydrogen processing of scrap magnets has been demonstrated as an extraction method for NdFeB from automotive rotors for the first time, with the aim to …Nov 15, 2021 · After the hydrogen decrepitation process, the powders were pulverized by either He-jet milling or N 2-jet milling, obtaining a powder with a particle size of ~0.8 µm for the HDDR processed and He-jet milled sample, ~1.0 µm for the He-jet milled sample, and ~3.0 µm for the N 2-jet milled sample.
Hydrogen decrepitation and recycling of NdFeB-type sintered magnets Zakotnik M, Devlin E, Harris IR, Williams AJ ... Environmental degradation of NdFeB magnets Yan GL, McGuiness PJ, Farr JPG, Harris IR Journal of Alloys and Compounds 2009;478:188-92 Oxidation of NdFeB-type magnets modified with additions of Co, Dy, Zr and V ...Dec 25, 2017 · Recycling of Nd-Fe-B magnets is one of the few solutions to alleviate the supply risks of certain rare earth elements (REE) such as Nd and Dy. One of the most promising solutions with regards to extraction of end-of-life (EOL) magnets is to apply hydrogen decrepitation and to physically separate the Nd-Fe-B as a demagnetized hydrogenated powder.
Nov 15, 2021 · After the hydrogen decrepitation process, the powders were pulverized by either He-jet milling or N 2-jet milling, obtaining a powder with a particle size of ~0.8 µm for the HDDR processed and He-jet milled sample, ~1.0 µm for the He-jet milled sample, and ~3.0 µm for the N 2-jet milled sample. The process of hydrogen decrepitation (HD), which is used in the primary production and recycling of Nd magnets, takes place at low temperatures, even at room temperature, so that the entire microstructure decomposes only in powder form and the grain size is reduced. The method combines hydrogen decrepitation (HD) disintegration of the initial magnet, powder sieving and the Press-Less Process (PLP), where hydride powder is sintered in a graphite mold. Coercivities up to 534 kA/m were obtained in porous samples based on powder size d < 100 µm. Adding a ball milling step resulted in full density …Rare earth magnets based upon neodymium-iron-boron (NdFeB) are employed in many high tech applications, including h... Skip to main content. Sign In Create account . Journal Article OPEN ACCESS. THE USE OF THERMAL HYDROGEN DECREPITATION TO RECYCLE Nd-Fe-B MAGNETS FROM ELECTRONIC WASTE. Piotrowicz A; Pietrzyk S; …
Mar 1, 2019 · Fig. 1 shows the hydrogen decrepitation curves of Nd-Fe-B SC and SM at 288 K with different initial hydrogen pressure. Under the initial hydrogen pressure of 0.1–1 Mpa, the HD process composes of four stages of magnets surface activation, slow hydrogenation of Nd-rich grain boundary phase, quick hydrogenation of Nd 2 Fe 14 B main phase grains, and slow hydrogenation of inner part of the magnets.
Dec 20, 2020 · After the hydrogen decrepitation, the hydrogenated NdFeB powder needs to be purified to remove all the impurities. This purification process has to be done in an inert atmosphere to avoid oxidation. Various authors have noted that both oxygen and carbon have been shown to have detrimental effects on the sintering process for NdFeB ( Lopes et al ...
The scrap sintered Nd–Fe–B magnets were recycled as the raw materials for bonded magnets using the hydrogen decrepitation (HD) process. The HD powders have the lowest oxygen and hydrogen content by hydrogenation at 150 °C with 1 bar H2 pressure and dehydrogenation at 600 °C. The powders with the largest particle size (>380 μm) …2.1. Introduction of this section. HDDR treatment is used to obtain Nd-Fe-B magnet powders with good magnetic anisotropy and high coercivity [6,8,19].Therefore, HDDR treatment has been used to produce anisotropic bonded magnets for high-performance motors in automobiles and electronic devices [20,21].In typical HDDR …Jul 8, 2020 · The application of hydrogen decrepitation (HD) as a process for recycling Nd-Fe-B sintered magnets was reported in [ 6 ], in which the essential role of hydrogen in the recycling process was demonstrated. The obtained magnetic properties of the recycled magnet were ( BH) max = 290 kJ/m 3 (±5 kJ/m 3 ), Br = 1240 mT (±50 mT) and jHc = 830 kA/m ... Mar 1, 2019 · The Hydrogen Decrepitation process (HD) is used as an alternative method of powder preparation in the manufacturing process of sintered Nd Fe B magnets [ 1]. During the HD process a NdFeB-type material is hydrogenated by gaseous hydrogen at atmospheric (or elevated) pressure at room (or elevated) temperature. During the hydrogenation process, a volume expansion takes place, which promotes the formation of transgranular and intergranular cracks, causing the breakup of the material [29].Fig. 1 shows the different types of fracture that can occur during the hydrogen decrepitation process. The hydrogenation of the grain boundary phase can lead to an …Hydrogen absorption/adsorption properties of high coercivity NdDyFeCoNbCuB sintered magnets were determined. Hydrogenation kinetics were analyzed using both differential scanning calorimetry (DSC) and X-ray diffraction (XRD). Hydrogenation of the Nd-rich intergranular phase results in a rather broad and large peak …Oct 25, 2015 · End-of-life NdFeB magnets are important secondary RE sources. Several recycling methods for NdFeB magnets have been developed, such as direct reuse,4 hydrogen decrepitation (HD) and regeneration of new NdFeB,5–7 pyrometallurgical methods,8,9 hydrometallurgical methods,10–13 gas-phase extraction.
A combination of hydrogen decrepitation (HD) and jet milling (JM) has been used to produce powder for the processing of permanent magnets. The procedure has proved to be very successful for both Nd-Fe-B (Neomax) alloys and the ND-Dy-Fe-Nb-B high coercivity alloys. The magnets produced by the HD/JM process showed excellent coercivities when …For the second type, three popular techniques, hydrogen decrepitation (HD), HDDR, and MS are applied to produce magnetic powders with the waste magnets. Note that the resultant powders prepared from the three techniques are single crystal powders, textured polycrystalline powders, and random aligned polycrystalline powders, respectively. ...The ultrafine magnet waste (particle size < 1 µm) contained around 50% rare earths mainly in the form of hydroxides as they are generated from the hydrogen decrepitation. The major phases in ultrafine NdFeB waste were Nd(OH) 3, Fe 2 O 3 and Fe phases. When ultrafine magnet waste was leached with hydrofluoric acid, all the iron …Abstract. Some fully dense, sintered NdFeB-type magnets (employed in VCM disc drives) have been subjected to a recycling process using the hydrogen decrepitation (HD) process. After a brief milling treatment, the powder was aligned, pressed and re-sintered and this procedure was repeated four times with a progressive fall in the density …NdFeB-based alloys and magnets also react readily with hydrogen, and this has been exploited by the hydrogen decrepitation (HD) process [4]. During HD the material is exposed to hydrogen (at room temperature) and initially the Nd-rich phase absorbs hydrogen (represented approximately by Eq.Hydrogen absorption/adsorption properties of high coercivity NdDyFeCoNbCuB sintered magnets were determined. Hydrogenation kinetics were analyzed using both differential scanning calorimetry (DSC) and X-ray diffraction (XRD). Hydrogenation of the Nd-rich intergranular phase results in a rather broad and large peak …
Hydrogen is already used to process cast NdFeB in the Hydrogen Decrepitation (HD) process. The HD process is used extensively to reduce bulk (or strip) cast NdFeB ingots to friable, hydrogenated NdFeB granules/powder, prior to the production of jet milled powder which is then aligned, compressed and sintered to form fully dense …Finely divided loose Nd2Fe14BHx, x≤5, hydride powder (particle size ≤1 μm is synthesized by washing Nd2Fe14B crystallites embedded in calcium and other by‐products (during a reduction‐diffusion‐reaction performed using excess calcium) in water. The calcium reacts thereby with the water and produces, Ca+H2O CaO+H2, native …
Hydrogen decrepitation (HD) is based on the selective synthesis of neodymium hydrides though the reaction of hydrogen gas with neodymium located in the Nd-Fe-B magnet. HD process was originally designed and patented by Harris et al. (1979) as a way to break down SmCo and Sm 2(Co,Fe,Cu,Zr) alloys. 5 17.Rare earth magnets based upon neodymium-iron-boron (NdFeB) are employed in many high tech applications, including h... Skip to main content. Sign In Create account . Journal Article OPEN ACCESS. THE USE OF THERMAL HYDROGEN DECREPITATION TO RECYCLE Nd-Fe-B MAGNETS FROM ELECTRONIC WASTE. Piotrowicz A; Pietrzyk S; …Semantic Scholar extracted view of "A study of the effects of the addition of various amounts of Cu to sintered NdFeB magnets" by O. Ragg et al. ... from an Nd/sub 17/-Fe/sub 76.5/-B/sub 5/-Cu/sub 1.5/ alloy by a two-step heat treatment at 1370 K and 870 K following hydrogen decrepitation (HD)-processing. …Hydrogen Decrepitation and Recycling of NdFeB-type Sintered Magnets. Miha Zakotnik, E. Devlin, +1 author. A. Williams. Published 2006. Materials Science, Engineering. Journal of Iron and Steel Research International. View via Publisher. Save to Library.Feb 1, 1997 · Hydrogen decrepitation of Nd-Fe-B type magnet alloys is a two stage process. Firstly, the hydrogen reacts with the Nd-rich phase at or close to room temperature. This is an exothermic reaction [4] and the heat evolved then allows the second stage to proceed in which the hydrogen is absorbed by the Nd^FeuB matrix phase. Hydrogen Decrepitation is a process step used in the production of Neodymium magnets to create extremely small grains in the material. Neodymium magnets must have very small grains averaging about 5 micrometers in order to have the best magnetic properties. But the grain sizes after casting are much larger than that, so they must be ground down ...
Hydrogen absorption and desorption characteristics for high coercivity NdDyFeCoNbCuB sintered bulk magnets were studied, by differential scanning calorimetry (DSC) measurement and hydrogenation kinetics measurement. The DSC measurements showed that hydrogenation of Nd-rich phase occurred in the temperature range of …
Hydrogen decrepitation (HD) is based on the selective synthesis of neodymium hydrides though the reaction of hydrogen gas with neodymium located in the Nd-Fe-B magnet. …
Mar 1, 1985 · The hydrogen decrepitation (HD) process are studied in detail based on these results. The hydrogen absorption mechanism of Sm(CoFeCuZr) 7.6 alloy can be regarded as a hydrogen dissolution process without phase transformation. In addition, the existence of a large amount of fine grains in the SC has an adverse effect on the alignment, which can ... Abstract. In this paper we describe and discuss the use of hydrogen in the processing ofNdFeB-type magnets. The roles of hydrogen in the hydrogen decrepitation (HD) and hydrogenation, disproportionation, desorption and recombination (HDDR) processes are considered together with the characteristics of the magnets produced by …PDF (11 MB) Get e-Alerts SUBJECTS: Grain, Hydrogen, Hydrogenation, Magnetic properties, Organic reactions Abstract Regarding the restrictions recently imposed by China on the export of rare-earth elements (REEs), …May 11, 2020 · Metallurgical simulation and evaluation of the resource efficiency of whole production processes are of key importance for sound environmental impact assessments. Exergy dissipation analysis is suitable to quantify the theoretical limits of a process and pinpoint hotspots for improvements along the value chain. Production of NdFeB permanent magnets is evaluated herein using a simulation-based ... This paper studied the corrosion behavior of c ∥ and c ⊥ surfaces in sintered (Ce 0.15 Nd 0.85) 30 Fe bal B magnets. The conclusions are as follows: (1) The distribution of RE-rich phase is improved after Ce substitution compared with the sintered Nd-Fe-B magnets, and the value of A0 / A1 is approximate for both c ∥ and c ⊥ surfaces.Mar 1, 2019 · Fig. 1 shows the hydrogen decrepitation curves of Nd-Fe-B SC and SM at 288 K with different initial hydrogen pressure. Under the initial hydrogen pressure of 0.1–1 Mpa, the HD process composes of four stages of magnets surface activation, slow hydrogenation of Nd-rich grain boundary phase, quick hydrogenation of Nd 2 Fe 14 B main phase grains, and slow hydrogenation of inner part of the magnets. Oct 25, 2015 · End-of-life NdFeB magnets are important secondary RE sources. Several recycling methods for NdFeB magnets have been developed, such as direct reuse,4 hydrogen decrepitation (HD) and regeneration of new NdFeB,5–7 pyrometallurgical methods,8,9 hydrometallurgical methods,10–13 gas-phase extraction. room temperature in a custom-made gauge glass reactor, and the hydrogen decrepitation process was video-monitored in situ with a single frame camera at 0.1 frames per second (fps).Abstract. In this paper we describe and discuss the use of hydrogen in the processing ofNdFeB-type magnets. The roles of hydrogen in the hydrogen decrepitation (HD) and hydrogenation, disproportionation, desorption and recombination (HDDR) processes are considered together with the characteristics of the magnets produced by …NdFeB-based alloys and magnets also react readily with hydrogen, and this has been exploited by the hydrogen decrepitation (HD) process [4]. During HD the material is exposed to hydrogen (at room temperature) and initially the Nd-rich phase absorbs hydrogen (represented approximately by Eq.Abstract. In this paper we describe and discuss the use of hydrogen in the processing ofNdFeB-type magnets. The roles of hydrogen in the hydrogen decrepitation (HD) and hydrogenation, disproportionation, desorption and recombination (HDDR) processes are considered together with the characteristics of the magnets produced by …Fully dense, sintered NdFeB-type magnets have been subjected to the hydrogen decrepitation (HD) process. The resultant powder has been subsequently …
Sep 17, 2021 · It is therefore expected that cracks are decreased by performing hydrogen decrepitation at higher temperature. To confirm this, the relationship between T dec (23°C–600°C) and the crack density D c was investigated. Here, D c was estimated by dividing the crack length in an SEM image by the cross-sectional area of the same image. 0.5% -1%. Dysprosium (Dy) 0.8% -1.2%. The method of manufacture of Neodymium Iron Boron magnets is as follows: The Neodymium metal element is initially separated from refined Rare Earth oxides in an electrolytic furnace. The “Rare Earth” elements are lanthanoids (also called lanthanides) and the term arises from the uncommon oxide …The hydrogen decrepitation (HD) behaviors of various forms of the permanent magnet alloy Nd{sub 16}Fe{sub 76}B{sub 8} and stoichiometric composition Nd{sub 11.8}Fe{sub 82.3}B{sub 5.9} have been investigated to provide background information on the production of sintered magnets by the HD process. ... The procedure …NdFeB ingot exposed to hydrogen atmosphere due to the changes of hydride lattice parameters cracks. The process called HDDR (Hydrogenation - …Instagram:https://instagram. i 94 expired but i 797 is validts icons.woff2bandq lamp shadesbest time to buy jewelry at macy Hydrogen Decrepitation (HD) has been used as an efficient and economical method in producing coarse NdFeB powder. This article studied the effects of hydrogen on the Nd-Dy-Fe-B magnets, such as HD ...Fully dense, sintered NdFeB-type magnets have been subjected to the hydrogen decrepitation (HD) process. The resultant powder has been subsequently … no manpercent27s sky cargo bulkheaduta entertainment The scrap sintered Nd–Fe–B magnets were recycled as the raw materials for bonded magnets using the hydrogen decrepitation (HD) process. The HD powders have the lowest oxygen and hydrogen content by hydrogenation at 150 °C with 1 bar H2 pressure and dehydrogenation at 600 °C. The powders with the largest particle size (>380 μm) … radio en linea guatemala Hydrogen Decrepitation (HD) is a suitable method for recycling sintered neodymium-iron-boron magnets obtained from electronic scrap into a coercive powder [2][3][4][5][6][7][8][9]. ... Anisotropic ...Jan 1, 2007 · The rapid cooling of the strip flakes suppresses the growth of soft α-Fe branch crystal grains. The thickness of the strip flakes was about 0.25–0.35 mm. Hydrogen decrepitation (HD), which uses the expansion of hydrogen to break up the flakes, was followed by milling in a jet mill (JM). The particles were then accelerated to supersonic ... The hydrogen decrepitation (HD) process are studied in detail based on these results. The hydrogen absorption mechanism of Sm(CoFeCuZr) 7.6 alloy can be regarded as a hydrogen dissolution process without phase transformation. In addition, the existence of a large amount of fine grains in the SC has an adverse effect on the …